Dès lors que l’on travaille sur des étapes consistant à former de la tôle, il est très fréquent de recourir à l’emboutissage profond en milieu industriel, de la fabrication de pièces pour les voitures à celle d’éléments pour des appareils d’électroménager. Zoom sur un procédé productif, bien maîtrisé et adapté à de nombreuses exigences.
Définition : l’emboutissage profond, qu’est-ce que c’est ?
Sur le principe, l’emboutissage profond peut être comparé à la déformation plastique du matériau : dans la pratique, il s’agit de fabriquer une pièce avec une feuille ou plaque (flan). À l’aide d’un poinçon, d’une matrice ainsi que d’un serre-flanc, on peut aussi bien aboutir sur des résultats de forme circulaire que carrée, rectangulaire (et même des conceptions plus complexes), le tout sans perdre en épaisseur.
Afin de réussir un emboutissage profond, il faut en maîtriser les paramètres essentiels, qui sont les suivants :
- Les dimensions (diamètres) du flan et du poinçon
- Les rayons des bords du poinçon et de la matrice
- Le jeu entre le poinçon et la matrice
- L’épaisseur et la pression du flan
- La lubrification
Il est essentiel de choisir les bons matériaux dans l’optique de produire suffisamment de pièces dans les délais impartis ; le tout en respectant toutes les exigences qualitatives du cahier des charges.
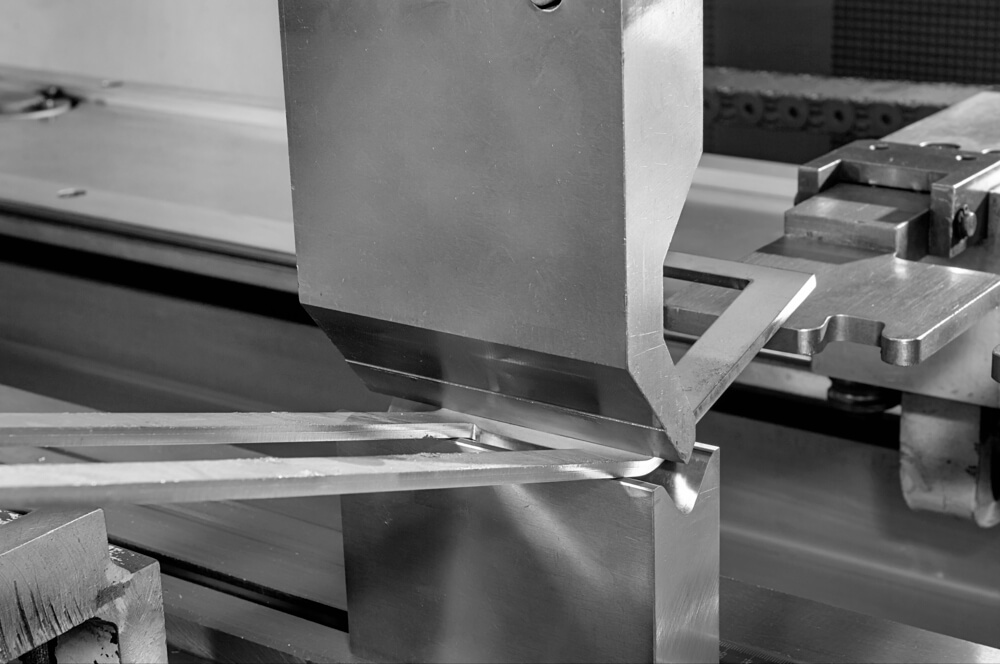
Maîtriser chaque étape pour un emboutissage profond réussi
Le jeu entre poinçon et matrice
Un jeu trop important entre ces deux parties pourrait générer des plis (également appelés « wrinkles »). C’est pourquoi on tolère un jeu de 10 % supplémentaires par côté pour les alliages à basse et moyenne résistance, avec 5 à 10 % de tolérance en plus pour les alliages plus solides.
Des rayons soignés pour un écoulement propre
Afin d’éviter à nouveau la formation de plis, il faut que les rayons des bords du poinçon et de la matrice facilitent l’écoulement des alliages : ils doivent être 4 à 8 fois plus épais que l’alliage à emboutir.
Respecter les exigences du cahier des charges en termes de finitions
Enfin, la rugosité des poinçons et matrices ainsi que le choix des lubrifiants respectent un cahier des charges précis.
Si vous avez besoin d’un accompagnement sur ce procédé, n’hésitez pas à vous adresser à un professionnel de la sous-traitance qui saura vous guider.